Basic Soldering For Electronics Pace Handbook Of Chemistry
Most of solder wires or solder paste contain lead (solder alloy is mixture of tin and lead). During soldering operation lead may produce fumes that are dangerous for your health. In addition, soldering wire usually has a flux in the middle of wire. There are different types of cored solder with different solder to flux rate. Flux containing rosin (colophony) produces solder fumes that, if inhaled, can be hazardous.
• Soldering should be performed only in a well-ventilated area.
• Use smoke absorber
• Soldering iron is very HOT (for most of soldering operation temperature of iron is 350 -400 degrees Celsius). Never touch tip of the soldering iron with your hand.
• Never leave your hot iron down on anything other than an iron stand.
• Keep flammable liquids and materials (such as alcohol, solvent etc.) away from the work area.
• Wear eye protection.
• Do not cut off a grounding prong on an iron plug to make it fit an ungrounded receptacle.
• Hold wires to be heated with tweezers, pliers or clamps to avoid receiving burns on your fingers from objects that are heated.
• Wear ESD (Electro-Static Discharge) protection if you are going to solder electro-static sensitive components such as CMOS components. For most of DIY projects it will be good enough to wear ESD wrist straps (shown on the picture below).
• Wash your hands with soap and water after soldering.
- Basic Soldering For Electronics Pace Handbook Of Chemistry Test
- Basic Soldering For Electronics Pace Handbook Of Chemistry Jobs
COURSE AGENDA. The hand soldering training course consists of five (5) 8-hour days for a total of 40 hours. The agenda for each day is outlined in this workbook. Retraining consists of two (2) 8-hour days for operators and inspectors.
- Physics and Chemistry (4 items) Knowledge of applied physics, including fluids, gasses, dynamic forces of levers, pneumatics, and hydraulics. Knowledge of basic chemistry as it applies to chemical measurement and control used in water treatment. Knowledge of chemical and physical properties of instrumentation applications.
- Companies and techniques. While basic solder theory e.g. The use of solder, heat and flux, remains largely intact across all applications, the applications themselves can vary greatly. Additionally, the use of different solder alloys and fluxes from company to company as well as from assembly to assembly requires.
I have a temperature controlled soldering station, and know that I need to set the temperature appropriately for soldering based on the solder I use when soldering, but how do I determine what temperature to use when de-soldering components from a commercially manufactured PCB?
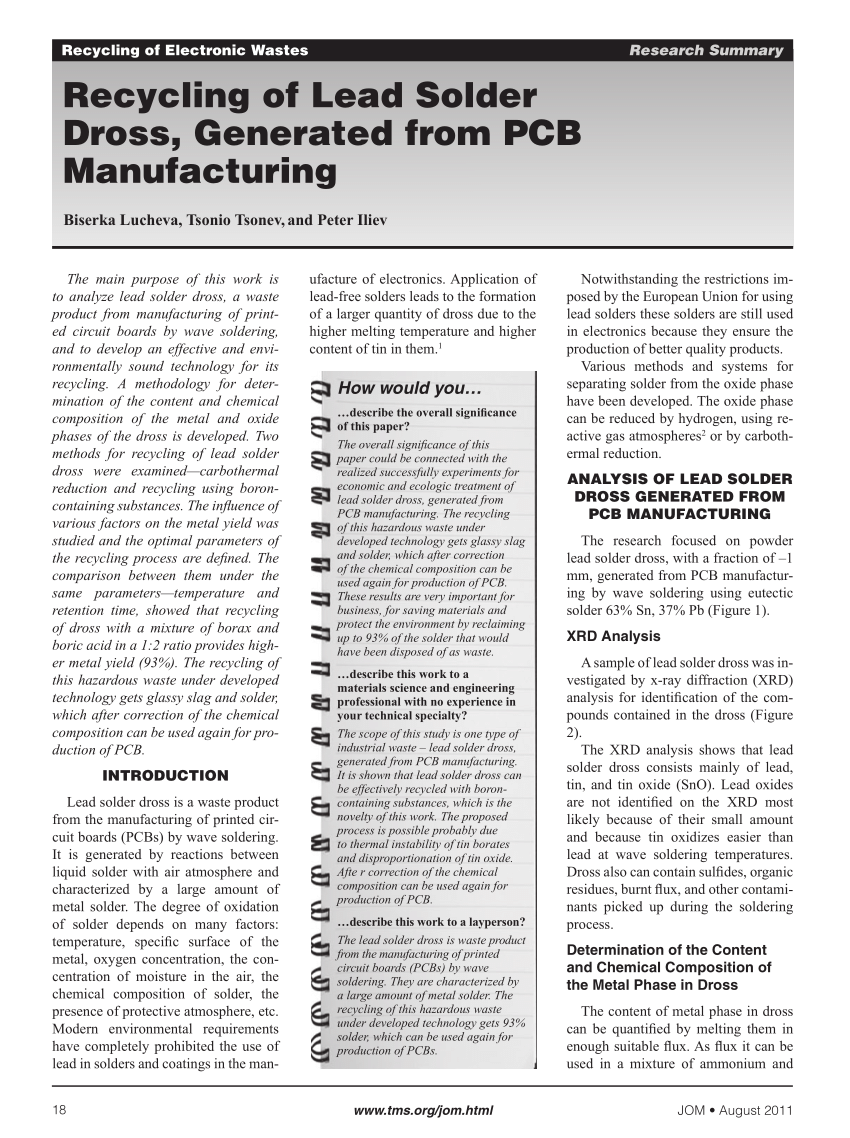
So far I have just been using 400°C and been careful not to heat for too long, but searches here on electronics and on the wider web have not been able to tell me how to work out what the ideal temperature for de-soldering would be.
Mark BoothMark Booth3 Answers
$begingroup$Desoldering in theory should utilize the same temperatures as soldering. Flux present during soldering helps reduce the required temperature. The same is true for desoldering, apply some flux to remove contaminants.
The melting point (per Weller) for various solder compositions is as follows:
Please note, these temperatures are melting points, not recommended soldering or desoldering iron temperatures.
Most guides recommend starting with the lowest temperature that will work in a short amount of time. This is a matter of opinion, but generally no less than 260°C (500°F).
The following factors will greatly affect desoldering performance:
- The type of solder used (lead-free requires higher temperatures)
- The age of the board and amount of contamination
- The number of layers in the board
- Size of ground/power/thermal planes connected to joint being desoldered
- Mass of component, leads, heatsink, etc.
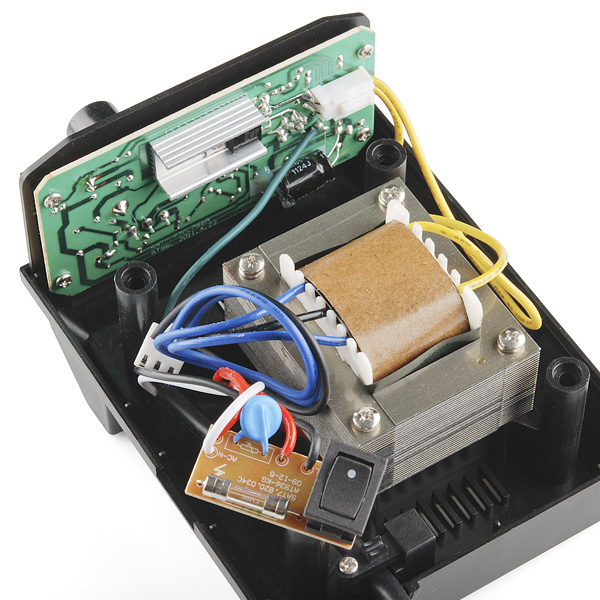
For example, desoldering a small through-hole component with small traces on a 2-layer board is much easier than desoldering the same component on a multi-layer board with large copper pours connected to the component. A larger component with more mass will require more time or more heat.
Think of it this way, if you set your temperature to 370°C (700°F) (a starting temperature recommended by Weller), the mass of solder and copper closest to the iron tip will heat quickly, but it will take some time for that heat to spread. If you are desoldering something with a heat sink or a ground plane, the extra mass will conduct heat away from the area of interest, and you must either apply the iron for a longer duration, or increase the temperature. The danger is that you may damage components if you exceed their temperature tolerance.
The Hakko 808 desoldering gun (which I use) ranges from 380-480°C (715-895°F). It does a remarkable job for most things, but I've occasionally needed to preheat a board for stubborn components that have a lot of mass or are connected to a heatsink.
Your temperature selection of 400°C (750°F) seems good. You could start at a lower temperature since you have the option, depending on the above factors.
JYeltonJYeltonBasic Soldering For Electronics Pace Handbook Of Chemistry Test
$endgroup$$begingroup$I generally start at around 650°F (340°C) for desoldering and work my way up. Wipe your tip on the soldering sponge first (makes it easier to melt) and heat the joint as fast as you can, taking care not to hold it there too long. If it's not working well, increase the temperature slightly and try again.
Remember if the temp on your iron is too low to melt the solder, then the person who built the board in the first place probably couldn't melt it either.
Basic Soldering For Electronics Pace Handbook Of Chemistry Jobs
I have always used 380°C-400°C to desolder. If you struggle with it, just add some of your own solder to the mounted components, always works for me. Of course, SMD components with many pins is a bit harder. With them I just heat the board on my stove and remove them after a while. Using an IR temperature reader should make you able to adjust this method quite precisely.
Ricardo